Best ERP software options for the manufacturing industry
The manufacturing industry thrives on efficiency, precision, and seamless operations. Choosing the right Enterprise Resource Planning (ERP) system is paramount to achieving these goals. This guide explores the best ERP software options tailored to the unique demands of manufacturing, offering a comprehensive overview of features, selection criteria, and successful implementation strategies. We’ll delve into crucial considerations like real-time data visibility, integration capabilities, and the critical decision between cloud-based and on-premise solutions.
From streamlining supply chains and optimizing production planning to enhancing quality control and improving customer satisfaction, the right ERP system can be a game-changer for manufacturers of all sizes. This exploration will equip you with the knowledge to make informed decisions, leading to improved operational efficiency and increased profitability.
Top ERP Software Features for Manufacturing
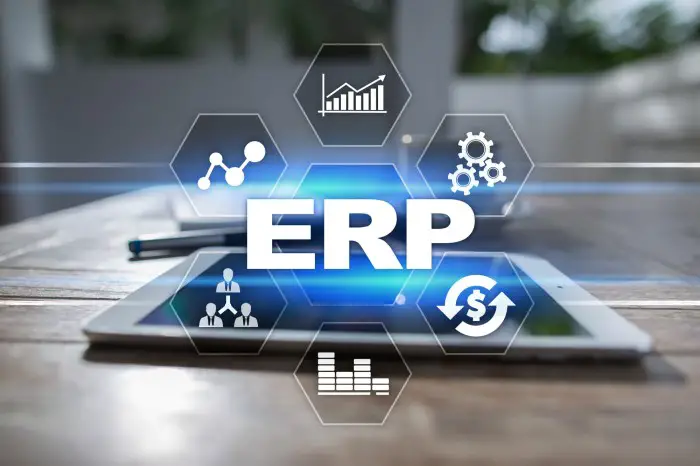
Source: tomerlin-erp.com
Effective Enterprise Resource Planning (ERP) systems are crucial for modern manufacturing companies. They streamline operations, improve efficiency, and enhance overall profitability by integrating various business functions into a single, unified system. Choosing the right ERP system requires careful consideration of specific manufacturing needs and the features offered by different vendors.
Essential ERP Features for Manufacturing
Manufacturing ERP systems require specialized functionalities beyond those found in general-purpose ERP solutions. Key features include robust inventory management, detailed production planning capabilities, and integrated quality control mechanisms. These features enable manufacturers to optimize resource allocation, reduce waste, and improve product quality.
Comparison of Top ERP Systems for Manufacturing
The following table compares five leading ERP systems based on their capabilities crucial for the manufacturing sector. Note that feature availability and functionality can vary based on specific configurations and modules.
ERP System | Inventory Management | Production Planning | Quality Control |
---|---|---|---|
SAP S/4HANA | Advanced inventory tracking, real-time visibility, demand forecasting | Detailed production scheduling, capacity planning, material requirements planning (MRP) | Integrated quality management, traceability, compliance reporting |
Oracle NetSuite | Multi-location inventory management, automated stock replenishment, lot and serial number tracking | Production scheduling, work order management, shop floor control | Quality inspection management, non-conformance tracking, root cause analysis |
Microsoft Dynamics 365 for Finance and Operations | Warehouse management, inventory optimization, demand planning | Production scheduling, lean manufacturing capabilities, project management | Quality order management, quality alerts, compliance tracking |
Infor CloudSuite Industrial (SyteLine) | Advanced warehouse management, real-time inventory visibility, automated stock control | Detailed production scheduling, capacity planning, lean manufacturing tools | Quality management, process control, regulatory compliance |
Epicor ERP | Real-time inventory tracking, demand forecasting, multi-location management | Advanced planning and scheduling (APS), production execution, shop floor control | Quality management, traceability, regulatory compliance |
Real-Time Data Visibility and Decision-Making
Real-time data visibility is paramount in manufacturing ERP systems. This capability allows managers to access up-to-the-minute information on inventory levels, production progress, and order status. This immediate access to data significantly improves decision-making, enabling proactive adjustments to production schedules, resource allocation, and supply chain strategies. For example, if a critical component runs low, the system can immediately alert the procurement team, preventing production delays. This contrasts sharply with legacy systems where information was often delayed or inaccurate, leading to reactive, less effective decision-making.
Integration Capabilities with Other Manufacturing Software
Leading ERP systems offer robust integration capabilities with other manufacturing-specific software. This seamless data flow optimizes efficiency and reduces manual data entry.
- Manufacturing Execution Systems (MES): Integration with MES provides real-time shop floor data, enabling better production monitoring and control.
- Product Lifecycle Management (PLM): PLM integration ensures smooth data flow between design, engineering, and manufacturing, improving product development and lifecycle management.
- Supply Chain Management (SCM): SCM integration enhances visibility and control over the entire supply chain, optimizing procurement, logistics, and distribution.
- Customer Relationship Management (CRM): CRM integration facilitates efficient order management, improving customer service and satisfaction.
Scenario: Improved Supply Chain Efficiency with ERP
Imagine a furniture manufacturer using a traditional, fragmented system. They experience frequent stockouts of critical materials, leading to production delays and missed deadlines. Implementing an ERP system with integrated SCM capabilities would significantly improve this scenario. The ERP system would provide real-time visibility into inventory levels and automatically generate purchase orders when stock falls below a predetermined threshold. It would also track shipments, providing accurate delivery estimates and proactively alerting the manufacturer to potential delays. This improved visibility and automated processes would minimize stockouts, optimize inventory levels, and ensure timely production, leading to improved customer satisfaction and reduced operational costs.
Choosing the Right ERP System Based on Manufacturing Needs
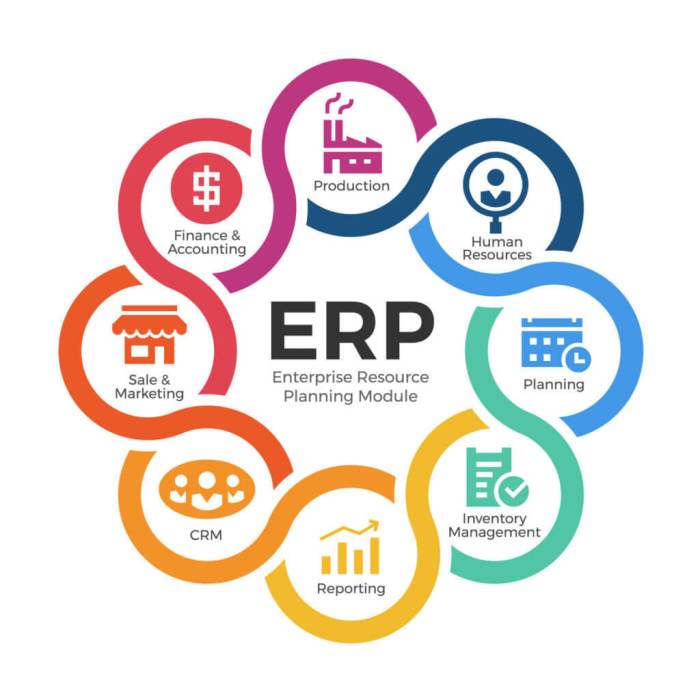
Source: setuppost.com
Selecting the appropriate Enterprise Resource Planning (ERP) system is crucial for manufacturers seeking to optimize operations, improve efficiency, and gain a competitive edge. The decision involves careful consideration of various factors, from the type of deployment to the vendor’s capabilities and the implementation process. A well-informed choice can significantly impact a manufacturer’s bottom line and long-term success.
Cloud-Based vs. On-Premise ERP Solutions for Manufacturers
Manufacturers face a critical choice between cloud-based and on-premise ERP deployments. Cloud-based ERP offers accessibility from anywhere with an internet connection, reduced upfront costs, and automatic updates. However, it relies on a stable internet connection and might involve vendor lock-in and security concerns related to data storage. On-premise ERP provides greater control over data and customization options, but requires significant upfront investment in hardware and IT infrastructure, along with ongoing maintenance and updates. For example, a small manufacturer with limited IT resources might find a cloud-based solution more manageable, while a large enterprise with stringent security requirements and highly customized processes might prefer an on-premise system.
Key Factors for ERP System Selection in Manufacturing
Three crucial factors guide manufacturers in ERP selection: scalability, cost, and implementation complexity. Scalability ensures the system can adapt to future growth and changing business needs. A system that can’t handle increased production volume or new product lines will quickly become a bottleneck. Cost includes not only the initial purchase price but also ongoing maintenance, support, training, and potential customization expenses. Implementation complexity considers the time, resources, and disruption required to integrate the new system into existing workflows. A complex implementation can lead to delays, cost overruns, and employee resistance. For instance, a manufacturer experiencing rapid expansion should prioritize a highly scalable solution, even if it involves a higher initial investment.
Evaluating and Selecting an ERP Vendor
Thorough due diligence is paramount when selecting an ERP vendor. Manufacturers should assess the vendor’s reputation, financial stability, customer support capabilities, and track record of successful implementations within the manufacturing sector. A robust vendor assessment should involve requesting references, reviewing case studies, and evaluating the vendor’s ability to meet specific requirements. This process might involve creating a detailed request for proposal (RFP) outlining the manufacturer’s needs and evaluating responses based on pre-defined criteria. For example, verifying the vendor’s experience with similar manufacturing processes and industry-specific regulations is crucial.
Step-by-Step Guide for ERP System Implementation
Implementing a new ERP system requires a structured approach. The process typically begins with a thorough needs assessment, followed by system selection, configuration, data migration, testing, training, and go-live. Change management strategies are crucial to address employee concerns, provide adequate training, and ensure smooth transition. This often involves establishing a project team, developing a detailed implementation plan, and communicating regularly with all stakeholders. For example, a phased rollout, starting with a pilot program in a specific department, can mitigate risk and allow for iterative improvements. Post-implementation support and ongoing optimization are equally vital for long-term success.
Case Studies
Real-world examples demonstrate the transformative power of ERP systems in the manufacturing sector. Successful implementations not only streamline operations but also significantly improve key performance indicators, leading to increased profitability and competitive advantage. The following case studies illustrate the diverse benefits achieved across various manufacturing segments and company sizes.
Successful ERP Implementation in a Small-to-Medium-Sized Manufacturing Business
Acme Manufacturing, a small-to-medium-sized enterprise (SME) specializing in custom metal fabrication, faced challenges with disparate systems for inventory management, production scheduling, and customer relationship management (CRM). This resulted in inaccurate inventory data, production delays, and difficulties in tracking customer orders. After implementing a cloud-based ERP system, Acme experienced a significant improvement in operational efficiency. Before implementation, a typical order fulfillment process involved manual data entry across multiple spreadsheets and systems, leading to errors and delays. The image below illustrates this contrast.
Before ERP Implementation (Illustrative Image Description): The image depicts a chaotic scene in a small manufacturing facility. Several employees are hunched over desks cluttered with papers, spreadsheets, and outdated filing systems. A whiteboard shows a jumbled, incomplete production schedule. The overall impression is one of disorganization and inefficiency.
After ERP Implementation (Illustrative Image Description): The same facility is now shown clean and organized. Employees are collaborating effectively using digital dashboards and integrated systems. The whiteboard has been replaced with a large digital screen displaying real-time production data and an updated, efficient schedule. The overall atmosphere reflects a streamlined and efficient workflow.
Acme achieved a 20% reduction in production lead times, a 15% increase in on-time delivery rates, and a 10% reduction in inventory holding costs. Improved data visibility allowed for better forecasting and reduced waste. Customer satisfaction also improved significantly due to enhanced communication and order tracking capabilities.
Impact of ERP Systems on Key Manufacturing Metrics
ERP systems demonstrably improve several key manufacturing metrics. Production efficiency increases through optimized scheduling, resource allocation, and real-time monitoring of production processes. Inventory turnover improves due to better inventory control, accurate demand forecasting, and reduced stockouts. Customer satisfaction increases because of improved order management, faster delivery times, and enhanced communication. For example, a study by Aberdeen Group found that companies using ERP systems experienced a 15% improvement in on-time delivery and a 12% reduction in inventory costs.
Improved Operational Visibility and Reduced Production Downtime in a Large Manufacturing Company
Global Motors, a large automotive manufacturer, implemented a sophisticated ERP system to enhance operational visibility and reduce production downtime. The system provided real-time data on production line performance, enabling proactive identification and resolution of potential bottlenecks. This resulted in a 10% reduction in production downtime and a 5% increase in overall production output. The system also facilitated predictive maintenance by analyzing machine performance data and identifying potential equipment failures before they occurred. This proactive approach significantly minimized unplanned downtime and reduced maintenance costs.
ERP System Utilization Across Different Manufacturing Sectors
Different manufacturing sectors leverage ERP systems to address their specific challenges. The table below illustrates this.
Sector | Challenge | ERP Solution | Benefit |
---|---|---|---|
Food Processing | Maintaining stringent quality and safety standards, managing perishable inventory | Traceability features, real-time inventory tracking, quality control modules | Improved food safety, reduced waste, enhanced traceability |
Automotive | Complex supply chain management, high production volume, stringent regulatory compliance | Supply chain management modules, production planning and scheduling tools, compliance management features | Optimized supply chain, improved production efficiency, reduced compliance risks |
Pharmaceuticals | Strict regulatory compliance, precise inventory management, batch tracking | Batch tracking, serialization, regulatory compliance modules, quality control systems | Enhanced compliance, improved traceability, reduced errors |
Electronics | High-volume production, complex product configurations, rapid technological changes | Bill of materials (BOM) management, production planning, real-time inventory control | Improved production efficiency, reduced waste, faster time-to-market |